7 Mitos sobre APS
Algo que chama a atenção do público acadêmico e profissional é a falta de bibliografia que disserte especificamente sobre o assunto APS. E basicamente o que se encontra na internet são materiais com viés comercial (viés que buscamos não prejudicar conteúdos como esse no nosso blog, mas enfim, aqui estamos). A consequência natural desse fato é a limitação do conhecimento do grande público sobre o assunto, que acaba se inteirando do APS de duas maneiras basicamente: na prática, realmente fazendo uso e/ou implantando uma solução destas no seu trabalho com auxílio de uma consultoria especialista; ou no boca-a-boca, falando com o pessoal do primeiro grupo ou até assistindo uma palestra em algum evento. E é assim que os mitos surgem. Vamos ver alguns deles:1. Com o APS, vou deixar de atrasar os meus pedidos e de gerar rupturas de estoques.Ao contrário da piada que nos ensina a colocar 50 palhaços dentro de um táxi, uma fábrica não tem capacidade infinita. Possivelmente o grande truque do APS seja realmente trabalhar com capacidade finita, ou seja, considerar os limites e restrições de um sistema produtivo para poder avaliar o que será possível produzir dentro dos prazos desejados ou não. Ao mesmo tempo o APS buscará fazer isso de uma maneira otimizada dentro das heurístisticas escolhidas, o que realmente gera mais eficiência e permite fazer mais com o mesmo (ou com menos).Porém, essa última vantagem faz que com algumas pessoas pensem que os atrasos simplesmente vão sumir, assim como as rupturas de quem produz para estoque. Em alguns casos existe claramente uma falta de capacidade e, mesmo otimizando a programação da fábrica, a mesma não será suficiente para atender a demanda. Nestes casos, o APS acabará sendo útil para simular incrementos de capacidade em setores específicos e auxiliar no Planejamento de Capacidade (Capacity Planning) para que, no médio/longo prazo, realmente os atrasos e rupturas sejam eliminados.2. O APS vai programar sozinho minha fábrica toda a vez que houver algum imprevisto na minha produção ao longo do dia.O processo de programação dentro de um software APS é algo está em constante melhoria, que parte de um processo prático e eficaz para o PPCP ter agilidade e bons resultados desde o marco-zero do uso, e evolui gradativamente com automações que apenas vão sendo captadas a partir do uso contínuo da solução. No limite, podemos chegar ao ponto de gerar uma programação totalmente autônoma, que não depende de intervenção humana. Porém, este é um longo caminho e, mesmo assim, é um processo discreto e com limites.Na grande maioria dos casos, o usuário APS realiza a programação uma a duas vezes ao dia, e quando há um grande imprevisto na fábrica, seja uma quebra de máquina ou um pedido para-quedas. É inclusive importante que não ocorra uma reprogramação constante minuto a minuto, caso contrário a programação fica, como chamamos, muito “nervosa”, mudando de sequência a todo momento. Nesse sentido, é bom ter um horizonte congelado de programação e buscar evitar mudanças contínuas na mesma. No final das contas, se houver algum problema pontual de curto prazo no chão-de-fábrica, quem irá resolver isto será a própria fábrica.3. O APS só funciona se tivermos 100% dos cadastros de engenharia atualizados e corretos.Esta constatação é possivelmente a mais recorrente e a que nunca será verdade. Nenhuma indústria terá sempre 100% de seus cadastros corretos e atualizados (aqui falamos de cadastros de engenharia como roteiros de fabricação com tempos de processo e alternativas de recursos, assim como estruturas de produto). Como uma fábrica também está em constante mudança, até mesmo um ótimo estudo pode estar defasado após apenas 3 meses.Para minimizar os impactos destas imperfeições intrínsecas à realidade, o ideal é controlar a aderência da programação, ou seja, o quanto estão executando o que está sendo programado. Caso esta aderência esteja baixa, os principais motivos podem ser regras de programação mal-concebidas, resistência no chão-de-fábrica para seguir a programação por disputa de poder, indicadores de desempenho de produção incoerentes, ineficiências, ou tempos e grupos de recursos com problemas cadastrais. Isolando os demais motivos, é possível identificar onde seus cadastros podem estar com mais problemas e realizar forças-tarefa para resolvê-los.Por último, o uso do APS também é muito eficaz para identificar problemas pois ele é muito visual. Caso, por exemplo, um tempo de produção esteja muito acima do que deveria ser, o próprio gráfico de Gantt já indicará o problema no flagra, mostrando uma operação superior às demais.[caption id="attachment_2065" align="aligncenter" width="522"]
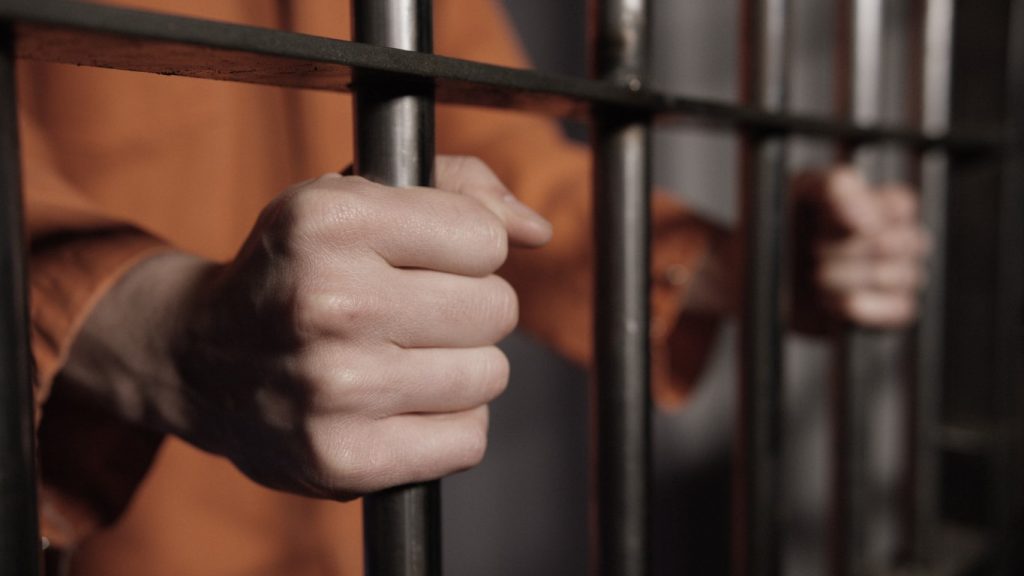
Se depender de todos os cadastros antes de começar, provavelmente não começará nunca.[/caption]4. O APS vai me ajudar a analisar a minha eficiência histórica (OEE) e diagnosticar que problemas tenho na produção.A palavra “programação” já infere que se trata do tempo futuro. Um sistema APS é focado em programar ordens/demanda no período futuro. Ou seja, nesse processo, o passado não é protagonista. É claro que ele pode auxiliar, principalmente o passado de curto prazo. A NEO utiliza os apontamentos de chão-de-fábrica de curto prazo para gerar visões de aderência da programação (KPI comentado no item anterior), o que é extremamente útil.Porém não se pode ter a expectativa de que o APS armazenará um histórico de anos e trará análises detalhadas deste histórico. Tecnicamente, é totalmente possível, porém já se trata de um outro escopo de solução, muito mais voltada para o Controle da Produção e os sistemas MES (Manufacturing Execution Systems).5. O APS só funciona se tiver uma solução de Controle de Produção (MES) em uso. Um sistema MES é importante para ter um panorama da produção em tempo real (ou o mais atualizado possível), porém, assim como foi no mito 2, a programação é realizada normalmente uma a duas vezes ao dia. Ou seja, se o key-user programa às 08h e às 13h, o que realmente é necessário é que o cenário do que foi produzido até aquele momento esteja atualizado, e não que tudo esteja atualizado a todo momento. Dessa forma, apontamentos em horários específicos de cada turno, ou apontamentos por unidades de movimento (pallet, bobina, etc) já são suficientes para uma boa programação fina no APS.6. O APS não é útil para linhas de montagem automotiva.Uma linha de montagem automotiva realmente não configura o uso tradicional de APS, porém há vantagens que podem ser muito positivas com o uso dele. Não haverá um sincronismo entre recursos e operações muito complexo causado por fluxos cruzados na produção que ocorrem em outros segmentos, porém existem problemas críticos de sincronismo de materiais. E o APS realiza este sincronismo e auxilia para que todos os processos adjacentes às linhas de montagem atendam-na da melhor maneira possível, identificando quando são necessários insumos em cada operação da linha, assim como em que momentos são imprescindíveis mudanças na linha devido a restrições de mão-de-obra, que podem causar paradas na linha e são tratadas no APS.No final das contas, devido à criticidade de manter o “tambor da fábrica” sempre eficiente, o uso do APS voltado para sincronismo de materiais e controle de restrições é de muita utilidade.[caption id="attachment_2064" align="aligncenter" width="610"]
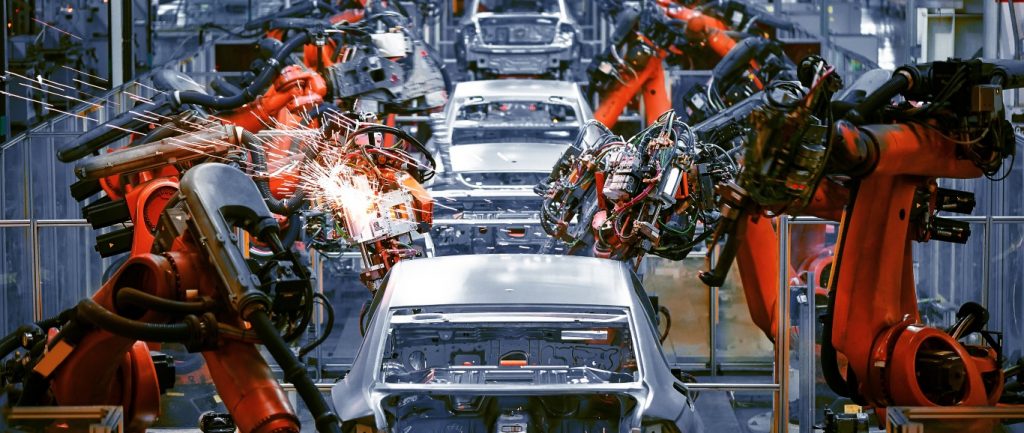
Linha automotiva[/caption]7. Não preciso de APS pois aqui implementamos o Lean Manufacturing System.Incrivelmente, conceitos que deveriam se somar de maneira sinérgica, muitas vezes são confundidos e entendidos como conflitantes. Além do Lean Manufacturing System se tratar de algo além de uma metodologia, mas uma filosofia, a mesma pode pode colaborar muito com o APS e vice-versa. O próprio exemplo do mito 6 já nos mostra isso, inserindo o APS em um ambiente que tradicionalmente respira Lean. Ao mesmo tempo, as análises de aderência que vimos no mito 3 podem ser matéria-prima para a organização de uma Kaizenblitz; a Troca Rápida de Ferramentas pode atualizar constantemente os tempos de setup utilizados pelo APS, e por aí vai.Ao mesmo tempo, o Lean, sozinho, não trata gargalos extretamente dinâmicos cada vez mais frequentes em ambientes produtivos em que o volume de SKUs e diversificação dos produtos aumenta vertiginosamente, fazendo com que, dependendo do mix a produzir, um setor pode ficar sobrecarregado e outro ocioso. Esse dinamismo exige uma resposta rápida e inteligente que apenas um sistema especialista é possível de fornecer, com heurísticas e um poder de simulação capazes de se adaptar a cada situação e momento das fábricas. Eis o APS.É claro que estes são apenas alguns dos mitos (sim, existem muitos mais!) e que os “crentes” destes nem sempre os defendem com unhas e dentes. Mas notamos, seja implícita ou explicitamente, que são questionamentos que rondam as mentes de quem estuda ou pratica o APS. A reflexão vale a pena para entender o que não esperar e o que não temer dele.Você já ouviu algum outro mito?! Compartilhe com a gente aqui![noptin-form id=2822]